È, questa, una frequente patologia del consulente, in generale, e dello specialista in tema di sicurezza sul lavoro, in particolare. Il suo nome risale alla leggenda mitologica del brigante greco
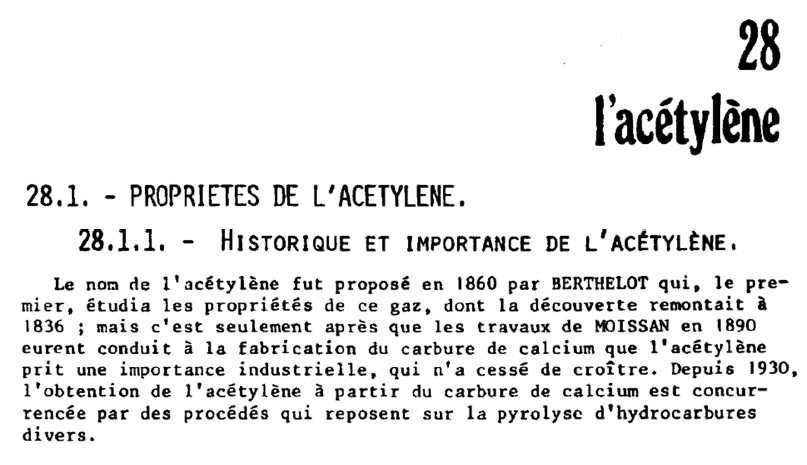
Il più antico tra i gas infiammabili moderni
Oggi discutiamo di alcune tra le proprietà dell’acetilene (etino), un idrocarburo diffusamente impiegato in vari settori industriali e scientifici. Certo, comprendo ci possano essere argomenti più interessanti. Tuttavia i gusti
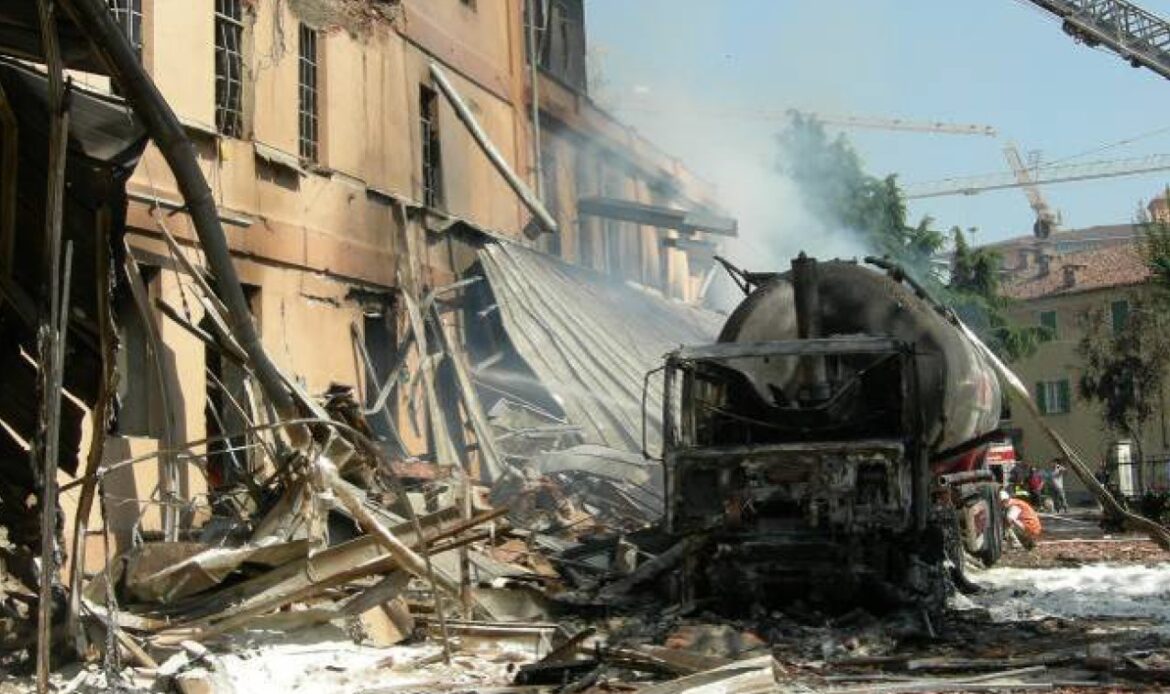
LE BARRIERE OCCULTE E LA SICUREZZA DEI PROCESSI INDUSTRIALI (ovvero del “non sapere di non sapere”)
Il 16 luglio 2007, a Fossano (CN), si verificò uno tra i peggiori incidenti industriali italiani di sempre. Ebbe luogo un’esplosione di polveri combustibili che, anche personalmente, creò una nuova
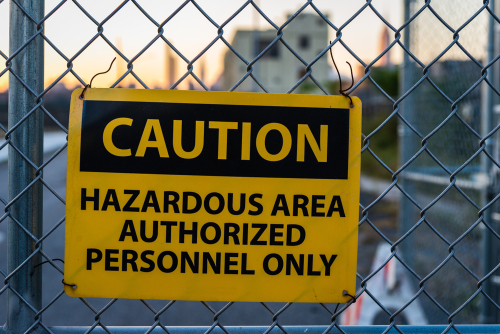
Zone non pericolose, zone NE e zone sicure. Sinonimi? Or Not?
Esistono, nell’ambito della normazione tecnica, problematiche che si evolvono e consolidano, nei decenni, a causa di lente ma prolungate “stratificazioni”. “Stalattiti” normative che, pian piano, con la loro crescita, possono
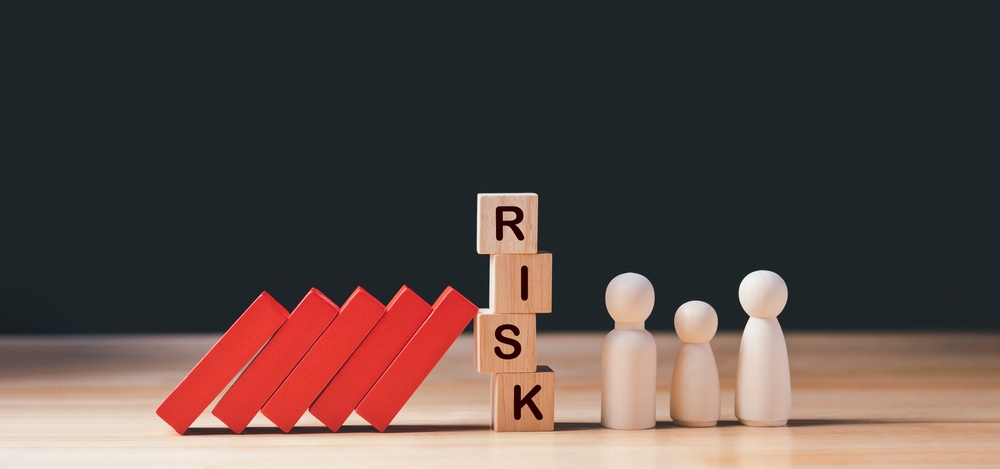
Del complottismo, del rischio e dell’ipocondria
Un post filosofico, oggi. Se si volesse dimostrare l’estinzione o meno di una specie, ci troveremmo di fronte a due compiti molto diversi. Per confermare che una specie è ancora
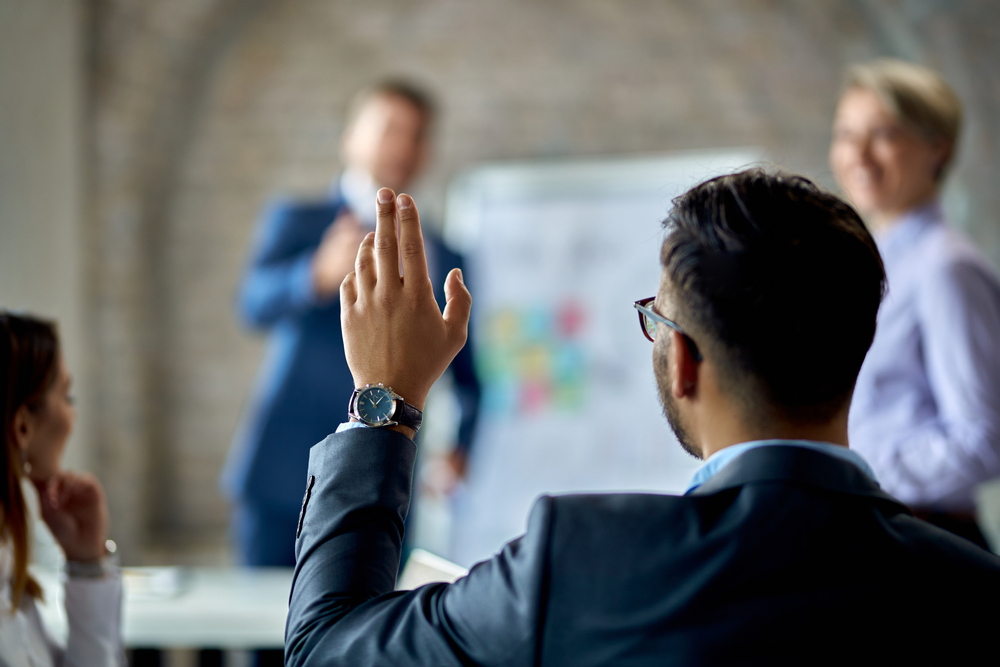
Q&A: Workshop ATEX 2024
Nel Workshop ATEX 2024, tenuto tra giovedì 29/2 e venerdì 1/3 (2024) sono nati parecchi spunti di riflessione. E domande. Che necessitavano di specifica risposta. Riepilogo, quindi, il Q&A del
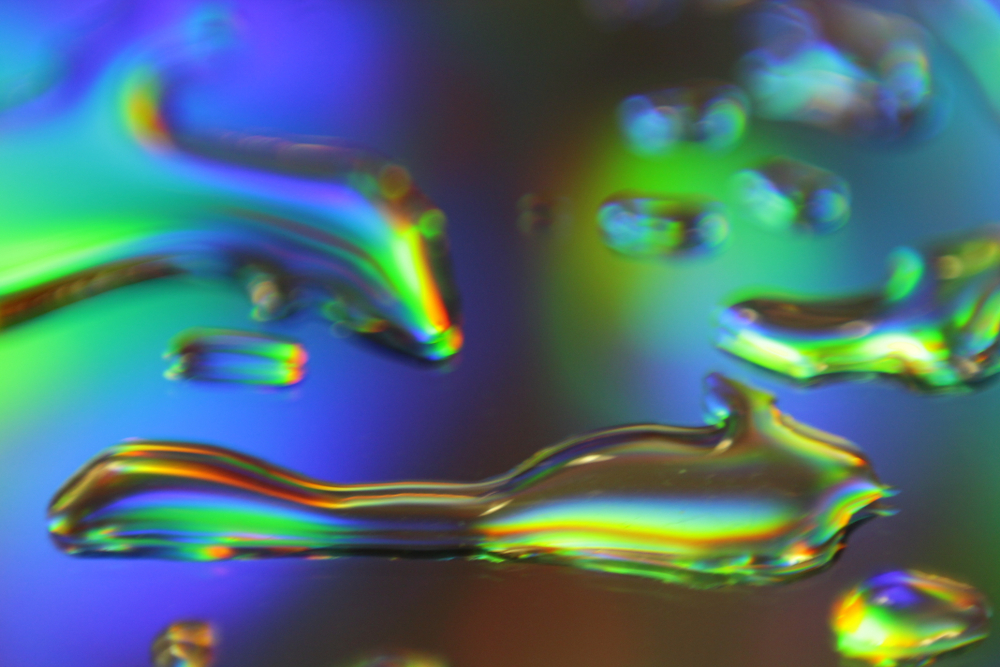
Delle pozze di infiammabili e dei “piccoli” problemi
Proviamo ad analizzare l’equazione di emissione da pozza presente nella terza edizione della Norma EN IEC 60079-10-1:2021. Come si vede, la portata risulta direttamente proporzionale alla velocità dell’aria che lambisce
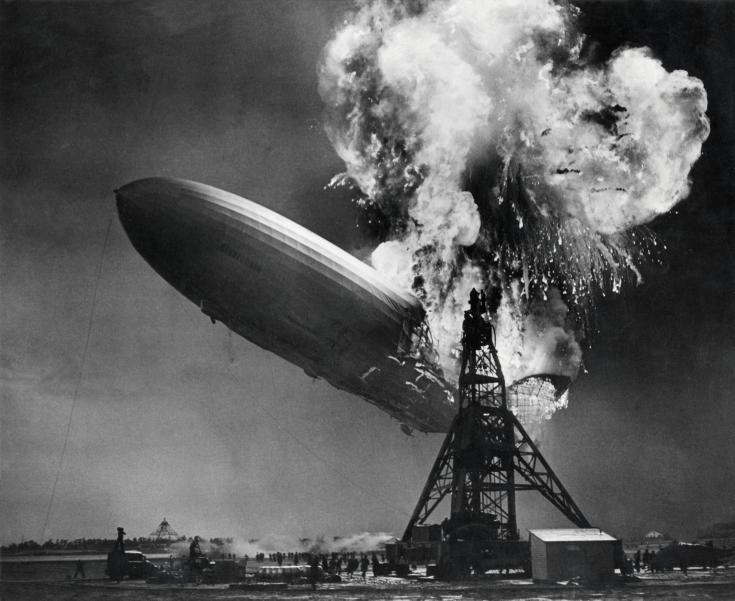
L’IDROGENO È SICURO: È LEGGERO E “VOLA VIA”
L’affermazione riportata nel titolo è corretta ma è necessario, come sempre in ambito ingegneristico, specificarne le condizioni al contorno. “Vola via” se: è rilasciato in spazio aperto; sono presenti moti
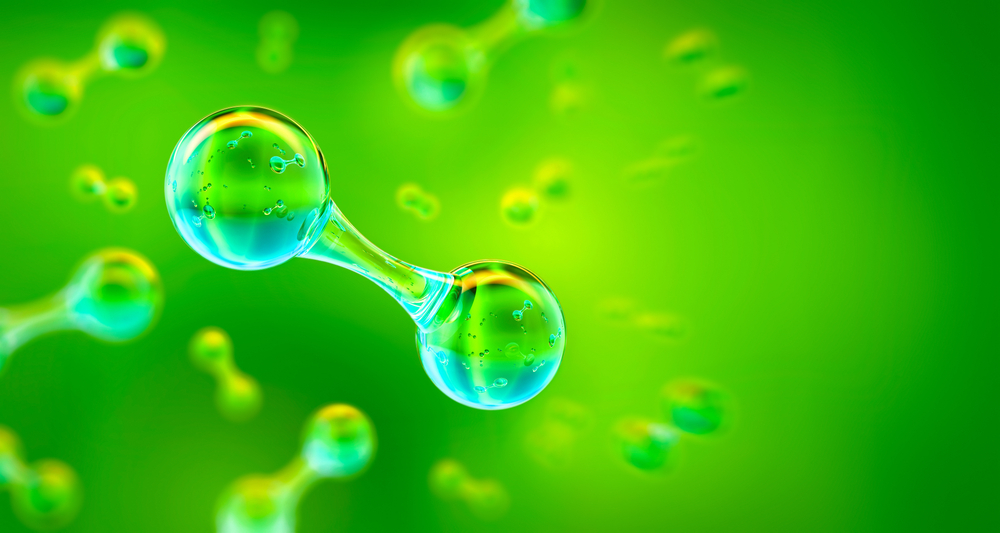
Dell’idrogeno nella rete gas e di altre pinzillacchere
Sono ormai diversi gli studi condotti sul blending gas, cioè su una ipotetica miscela di metano-idrogeno da convogliare nelle reti infrastrutturali con l’obiettivo principale di “risparmiare” gas naturale per la